Prozessintegriertes Mess- und Regelungssystem zur Ermittlung und sicheren Generierung von funktionsrelevanten Eigenschaften in Oberflächenrandzonen beim BTA-Tiefbohren (im SPP 2086)
Dieses DFG-geförderte Schwerpunktprogramm wird gemeinsam mit dem Fachgebiet Werkstoffprüftechnik (WPT) der TU Dortmund bearbeitet. Ziel des Forschungsprojekts ist es, das BTA-Tiefbohren (Boring and Trepanning Association), ein Verfahren zur Erzeugung von Bohrungen mit einem großen Länge-zu-Durchmesser-Verhältnis, mithilfe kombinierter In-Prozess-Sensorik zu untersuchen, um Prozess-Struktur-Eigenspannungs-Beziehungen in Abhängigkeit von der Oberflächenkonditionierung durch den Zerspanprozess zu ermitteln.
Aus Sicht der Zerspanungstechnologie verfolgt der Antrag das Ziel, wissenschaftliche Grundlagen und technologische Lösungen für ein gezieltes Einbringen von Eigenspannungen beim BTA-Tiefbohren mit prozessintegrierter Randzonenbeeinflussung zu erarbeiten, um die Oberfläche und die Bauteileigenschaften, wie z. B. die Schwingfestigkeit, gezielt zu beeinflussen und zu verbessern. Zur Erweiterung des Prozessverständnisses soll während des Bohrprozesses das thermomechanische Belastungskollektiv an den Wirkelementen des Werkzeugs ermittelt und analysiert werden.
Aus Sicht der Werkstofftechnik und -prüfung verfolgt der Antrag das Ziel, die Oberfläche zu konditionieren, mit dem Fokus, die Mechanismen der Eigenspannungsentstehung und Mikrostrukturänderung beim BTA-Tiefbohren und die Randzonenbeeinflussung von austenitischen Stählen auf mikrostruktureller Ebene zu verstehen, die Stabilität der Eigenspannungen und ihre Auswirkung auf die Bauteileigenschaften zu untersuchen und das quasistatische und zyklische Verformungsverhalten in Abhängigkeit von den induzierten Eigenspannungen mikrostruktur- und mechanismenbasiert zu charakterisieren. Zudem sollen etablierte Methoden der Eigenspannungsmessung auf Basis mikromagnetischer Sensorik (weiter-)entwickelt und experimentell im Sinne einer prozessintegrierten Sensorik und Prozessregelung validiert werden. Das gewonnene Prozessverständnis sowie die aufgenommenen und analysierten Messdaten bilden die Grundlage für eine Finite-Elemente-Simulation zur Vorhersage der resultierenden Bohrungsrandzone in Abhängigkeit von dem Schneiden- und Führungsleisteneingriff.
In der zweiten Förderperiode soll ein Sensorkopf für das Magnetische Barkhausenrauschen entwickelt werden, der in den Bohrkopf integriert bzw. auf das Werkstück appliziert wird, um die Oberflächeneigenschaften, z. B. anhand induzierter Eigenspannungen und Härteveränderungen, in-process mittels Softsensorik zu ermitteln. Anschließend soll durch ein in der ersten Förderperiode entwickeltes Prozessmodell die Prozessregelung dahingehend ertüchtigt werden, die angestrebten Eigenspannungswerte und Bauteileigenschaften auf Basis der in-process ermittelten Kennwerte während des Fertigungsprozesses einzustellen und Prozessparameter nachzuregeln, damit die geforderten Eigenschaften gezielt und reproduzierbar eingestellt werden können.
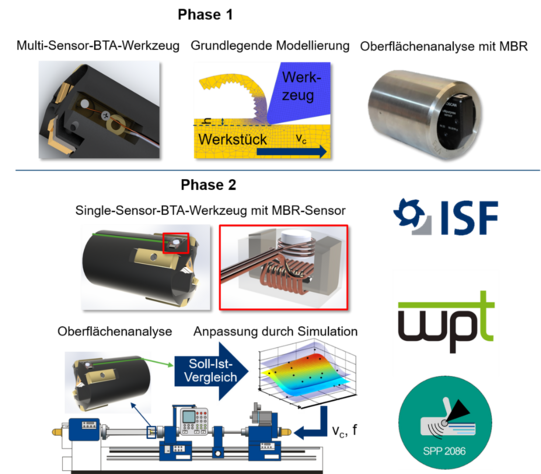