Process-Integrated Measuring and Control System for the Determination and Reliable Generation of Functionally Relevant Properties in Surface Edge Zones during BTA Deep Hole Drilling
This research project within the DFG-funded priority programme 2086 is jointly run by the ISF and the Department of Materials Test Engineering (WPT). Its aim is to investigate the BTA (Boring and Trepanning Association) deep hole drilling, a method for the generation of bores with a large length-to-diameter ratio, by using combined in-process sensor technology in order to determine process-structure-residual stress relationships as a function of surface conditioning by the machining process.
Especially the systematic generation of residual stresses in BTA deep hole drilling is focused. Therefore, process-integrated near surface zone control is applied in order to influence and improve the surface and component’s properties, such as vibration resistance. To extend the understanding of the process, the thermomechanical load spectrum at the active elements of the boring-head are to be determined and analysed during the drilling process.
From the point of view of materials engineering and testing, the project aims to condition the surface, focusing on the understanding of the mechanisms of residual stress generation and microstructural changes during BTA deep hole drilling. Furthermore, the surface integrity of austenitic steels at the microstructural level is investigated as well as the stability of the residual stresses and their effects on the component properties. To characterise the quasi-static and cyclic deformation behaviour as a function of the induced residual stresses based on microstructures and mechanisms, additional investigations are carried out. In addition, established methods of residual stress measurement on the basis of micromagnetic sensor technology are to be developed in the direction of process-integrated sensor technology and process control and experimentally validated.
The acquired process knowledge as well as the recorded and analysed measurement data form the basis for a finite element simulation for predicting the resulting surface edge zone as a function of the cutting edge’s and guiding-pad’s engagements.
In the second phase, a sensor head for the Magnetic Barkhausen Noise is to be developed, which will be integrated into the bore head or applied to the workpiece in order to determine the surface properties online during the process using soft sensor technology, i.e. based on induced residual stresses and changes in hardness. Subsequently, the process model developed in the first phase will be used to upgrade the process control system in order to achieve the desired residual stress values and resulting component properties.
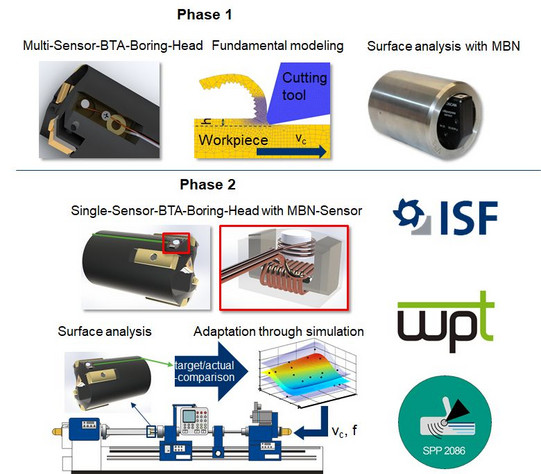