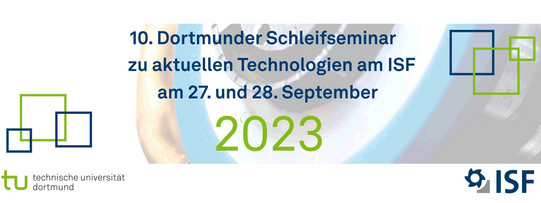
Einladung zum 11. Dortmunder Schleifseminar
Neue Werkstoffe und steigende Qualitätsanforderungen stellen Herausforderungen an die Zerspanung mit geometrisch unbestimmter Schneide, die sowohl in der Forschung als auch in der Industrie Weiterentwicklungen motivieren. Durch innovative Schleifwerkzeuge und angepasste Prozessentwicklungen finden Schleifprozesse nicht nur als Endbearbeitungsverfahren Anwendung, sondern können vielfältig in unterschiedlichen Anwendungsbereichen auch mit sehr hoher Produktivität eingesetzt werden. Darüber hinaus müssen aktuell und zukünftig immer intensiver die Energie- und Ressourcenverbräuche der Produktion betrachtet werden.
Das 11. Dortmunder Schleifseminar am 5. und 6. März 2026 fokussiert in diesem Kontext das Zusammenspiel zwischen praxisorientierten Entwicklungen und wissenschaftlichen Erkenntnissen. Zudem bietet es die Möglichkeit, Fachwissen zu erweitern und Netzwerke auszubauen. Mit qualifizierten und spannenden Beiträgen ermöglicht das Schleifseminar Einblicke in die kooperative Arbeit zwischen Industrie und Forschung. Die zweitägige Veranstaltung ist unterteilt in mehrere Vortragsblöcke und wird durch eine Besichtigung des Versuchsfeldes des ISF sowie einer Abendveranstaltung, die zur konstruktiven Diskussion und intensivem Austausch mit den Referenten und den Teilnehmenden Gelegenheit geben, ergänzt.
Ich freue mich darauf, Sie zur Jubiläumsauflage des Dortmunder Schleifseminars am Institut für Spanende Fertigung in Dortmund begrüßen zu dürfen.
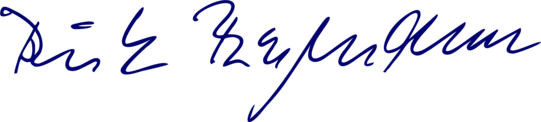

