Charakterisierung und Modellierung des Verschleißverhaltens beschichteter Hartmetallwerkzeuge bei der Drehbearbeitung eines schwer zerspanbaren Stahlwerkstoffes
Aufgrund des voranschreitenden Klimawandels und den daraus resultierenden Restriktionen für den globalen CO2-Ausstoß besteht die Forderung nach einer prozesssicheren, produktiven und insbesondere ressourcenschonenden spanenden Bearbeitung industrieller Güter. In diesem Kontext ist der Verschleiß der Zerspanungswerkzeuge von zentraler Bedeutung, da er sowohl Einfluss auf die Prozesssicherheit als auch auf die Produktivität nimmt. Der Begriff Verschleiß umfasst dabei ein komplexes Kollektiv an Mechanismen, die in Form verschiedener Erscheinungsformen geometrische und stoffliche Veränderungen am Werkzeug hervorrufen. Diese Mechanismen unterliegen diversen Abhängigkeiten, wie z. B. der Werkzeug-Werkstoff-Paarung oder dem thermomechanischen Belastungskollektiv in der Spanbildungszone, das wesentlich durch die Schnittwerte beeinflusst wird. Um Werkzeuge und Prozesse effizient optimieren und weiterentwickeln zu können, ist die detaillierte Kenntnis dieser Abhängigkeiten sehr entscheidend. Insbesondere für die Verwendung von Simulationssystemen, die heutzutage eine zeit- und ressourcenschonende Prozess- und Werkzeugentwicklung realisieren können, sind experimentell ermittelte Ergebnisse sowohl als Eingangsdaten für die Simulation als auch zur Validierung zwingend notwendig.
Im Rahmen dieses Projektes soll daher eine auf modernen Charakterisierungsmethoden basierende Modellierung des Verschleißes von beschichteten Hartmetallwerkzeugen bei der Zerspanung des austenitischen Stahls X2CrNiMo17-12-2 entwickelt und in eine Finite-Elemente-Simulation implementiert werden. Dazu werden zunächst Zerspanungsuntersuchungen mit einer Titannitrid- und einer Titanbornitrid-Beschichtung auf einer CNC-Drehmaschine durchgeführt, bei denen mithilfe von innovativen Messmethoden die Temperaturen auf der Span- und der Freifläche sowie der Werkzeugverschleiß gemessen werden. Im Anschluss sollen Versuche zur Charakterisierung des Reibungsverhaltens zwischen dem Werkstoff und den Beschichtungen durchgeführt werden, bei denen die Reib- und die Normalspannung unter zerspanungsähnlichen Bedingungen und Variation der Relativgeschwindigkeit gemessen werden. Die Ergebnisse dieser Untersuchungen werden in Kombination mit experimentell ermittelten Fließspannungsdaten genutzt, um ein Finite-Elemente-Modell der Spanbildung zu entwickeln. Aus diesem Modell, das mithilfe der mechanischen und thermischen Werkzeugbelastungen aus den Zerspanungsversuchen validiert wird, können die Relativgeschwindigkeiten und Drücke im Kontaktbereich zwischen Werkzeug und Werkstück bzw. Werkzeug und Span vorhergesagt werden. Durch eine kombinierte Analyse dieser Daten, mit den Ergebnissen der experimentell durchgeführten Temperatur- und Verschleißmessungen, werden im Anschluss Modelle der Verschleißrate in Abhängigkeit von der Beschichtung sowie der Temperatur, der Relativgeschwindigkeit und des Drucks berechnet. Zuletzt werden diese Modelle in die bestehende Simulation implementiert, sodass der Verschleiß bei der Drehbearbeitung vorhergesagt werden kann.
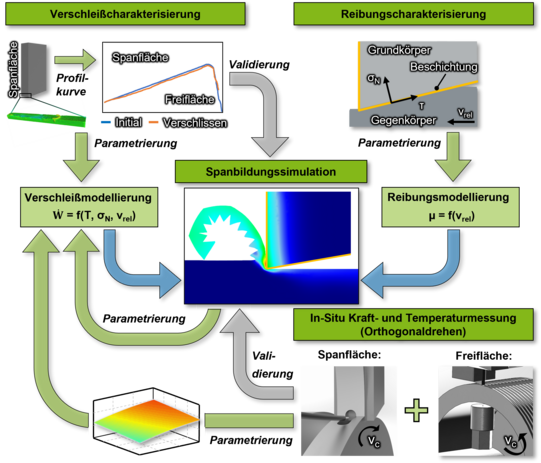