Simulationsbasierte Entwicklung und experimentelle Validierung von werkzeugintegrierten Rotations-Partikeldämpfern
Das Fräsen formgebender Werkzeugkomponenten aus Warmarbeitsstahl kann je nach gegebenen Prozessbedingungen mit ausgeprägten regenerativen Ratterschwingungen verbunden sein, die neben einem gesteigerten Werkzeugverschleiß u. a. signifikante Beschädigungen der Bauteiloberflächen zur Folge haben. Durchgeführte Grundlagenversuche zum Fräsen mit partikelgedämpften HSK63-Aufnahmen haben bereits aufgezeigt, dass applizierte Rotationspartikeldämpfer (RPD) einen vielversprechenden Ansatz darstellen, auftretende Werkzeugschwingungen zu reduzieren und somit auch bei üblicherweise schwingungskritischen Parametern einen prozesssicheren Materialabtrag ermöglichen. Daran anknüpfen soll in diesem von der Deutschen Forschungsgesellschaft (DFG) geförderten Forschungsprojekt die Entwicklung eines Wendeschneidplattenfräsers mit integrierten RPD erfolgen, der eine erhöhte Stabilität und folglich Fertigungsqualität bei der Funktionsflächen-bearbeitung im Werkzeug- und Formenbau ermöglicht. Basierend auf fundamentalen Simulationen der Partikeldynamik bei bestehender Werkzeugrotation, gestützt durch begleitende experimentelle Analogieversuche, lässt sich dabei in Kooperation mit dem Institut für Technische und Numerische Mechanik (ITM) der Universität Stuttgart eine systematische Konzeptionierung mit deutlich reduziertem Zeit- und Versuchsaufwand realisieren. Dieser kombinierte Ansatz, valide, durch die Analogieversuche generierte Messdaten zur Kalibrierung der Partikelsimulationen zu nutzen, ermöglicht einen grundlegenden Erkenntnisgewinn hinsichtlich der Partikelbewegung unter wirkender Zentripetalkraft und dadurch eine dissipationseffiziente Systemauslegung. Im Speziellen lassen sich somit konstruktive Maßnahmen zur Steigerung des Dämpfungsvermögens zielgerichtet durchführen. Beispielsweise ist die Applikation einer auf das vorliegende Partikelbewegungsmuster angepasste Innenstruktur mit einer Erhöhung potenzieller Kontaktflächen zwischen den Partikeln und Werkzeug und dadurch einer gesteigerten Dissipation der Schwingungsenergie durch inelastische Partikelstöße verbunden. Ergänzend dazu ermöglicht eine auf die Partikeldynamik abgestimmte Makrostrukturierung der RPD-Innenwandungen eine erhöhte Reibungsdissipation.
Zentraler Bestandteil der systematischen RPD-Auslegung ist neben dem zu entwickelnden Analogieversuchstand, der in Verbindung mit dem speziell gestalteten Analogiewerkzeug, das einen Blick ins Innere der RPD zulässt und somit die Möglichkeit zusätzlicher High-Speed-Videografieaufnahmen der Partikelbewegung bei Werkzeugrotation darbietet, die Verwendung von periodischen Rändern bei dem Simulationsaufbau. Durch diese Simulationsstrategie lassen sich die Rechenzeiten signifikant reduzieren, da lediglich repräsentative Teilbereiche des RPD detailliert zu betrachten und die Ergebnisse systematisch auf das gesamte Simulationsgebiet zu übertragen sind. Dieses Vorgehen wurde bereits bei translatorisch angeregten Systemen erfolgreich angewendet und ist unter Einbeziehung der im Rahmen der Analogieversuche ermittelten Messdaten auf die RPD zu adaptieren. Eine der größten Herausforderungen besteht dabei darin, eine geeignete Unterteilung des Simulationsgebiets zu finden um fundierte Simulationsergebnisse zu gewährleisten. In ersten Versuchen mit einem vereinfachten RDP-Aufbau ließ sich die Realisierbarkeit der vorgesehenen Simulationsgestaltung bereits grundlegend nachweisen (Abbildung).
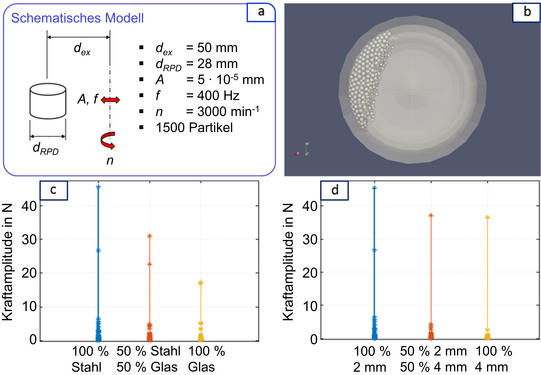