CoatingStruc – Innovativer, hybrider Herstellungsprozess texturierter, thermisch¬gespritzter Oberflächensysteme zur Verbesserung von Reibungskoeffizienten um bis zu 10%
Im Bereich der Oberflächentechnik haben sich thermisch gespritzte Schichtsysteme auf der Basis von Wolframcarbid (WC) zu einem etablierten Lösungsansatz entwickelt, um tribologisch beanspruchte Oberflächen gegen Verschleiß zu schützen. WC‐basierte Schichtsysteme, wie beispielsweise WC‐Co oder WC‐CoCr unter der Zugabe von Cobalt bzw. Chrom, werden überwiegend mittels des Hochgeschwindigkeitsflammspritzens (high velocity oxygen‐fuel (HVOF)) appliziert. Im Vergleich zu unbeschichteten Vergütungsstählen bieten HVOF‐gespritzte WC‐Hartstoffschichten unter Gleitbeanspruchung eine wesentlich verbesserte Verschleißbeständigkeit. Im flammgespritzten Zustand („as‐sprayed“) zeigt die erzeugte Schicht eine hohe Oberflächenrauheit, weshalb eine Nachbehandlung für viele Anwendungen zwingend erforderlich ist. In der industriellen Praxis wird hierzu meist ein kostenintensiver, häufig mehrstufiger mechanischer Nachbehandlungsprozess mittels Schleifen und Polieren eingesetzt.
Die Reibung zwischen tribologisch beanspruchten Oberflächen, wie beispielsweise Gleitflächen und Lagerstellen, kann in der Regel durch den Einsatz von Flüssigschmierstoffen signifikant reduziert werden. Um eine kontinuierliche Schmierung an Gleitflächen zu ermöglichen, kann durch die Funktionalisierung, also die gezielte Gestaltung der Oberfläche, die Schmierstoffzufuhr sowie der Schmierstofferhalt in der Kontaktzone gefördert werden. Die Applikation von Oberflächentexturen als Schmierstofftaschen kann hierbei die hydrostatische und hydrodynamische Gleitlagerung begünstigen. Dadurch kann der Reibungskoeffizient von texturierten Flächen unter Schmierstoffinteraktion, im Vergleich zu nicht‐texturierten Flächen, signifikant reduziert werden. Oberflächentexturierungen werden derzeit zumeist durch lasergestützte Verfahren realisiert, was Nachteile, wie Gratbildung und thermisch bedingte Defekte, in der Wärmeeinflusszone mitsichbringt. Für thermisch sensitive Materialien, wie beispielsweise WC‐Hartstoffschichtsysteme (insbesondere für submikroskopische oder nanoskalige WC Partikel), besteht ein erhöhtes Risiko von unerwünschten Phasenumwandlungsvorgängen, welche die mechanischen Schichteigenschaften und folglich die Standzeit der Schicht bei zyklischer, mechanischer Belastung signifikant negativ beeinflussen. Eine Alternative stellen spanende Fertigungsverfahren dar, welche die beschriebenen Nachteile in deutlich geringerem Maße aufweisen.
Durch einen neuartigen, hybriden Fertigungsprozess, bestehend aus dem Hochgeschwindigkeitsflammspritzen und der spanenden Nachbearbeitung mit geometrisch bestimmter Schneide (z. B. Mikrofräsen), soll das Ziel des Vorhabens, bionische & technische Texturen/Strukturen auf thermische Spritzschichten aufzubringen, erreicht werden. Dadurch lassen sich die oben genannten Nachteile vermeiden und die tribologischen Eigenschaften (z. B. Reibungskoeffizient) an das jeweilige Anwendungsumfeld anpassen. Hierfür müssen zum einen die Schichtzusammensetzung sowie die Mikrogefügestruktur für die Zerspanung optimiert und zum anderen die mechanische Nachbearbeitung auf die funktionalisierende Texturierung der beschichteten Oberfläche angepasst werden. Die neuartige Schichtarchitektur muss eine geringe Porosität (2 ‐ 10 %) bei anwendungsgerechten mechanischen Eigenschaften aufweisen. Die mechanische Nachbearbeitung bietet, neben der Vermeidung der Nachteile von lasergestützten Verfahren, sogar das Potential, gezielt Druckeigenspannungen einzubringen und damit die Ermüdungsfestigkeit zu steigern.
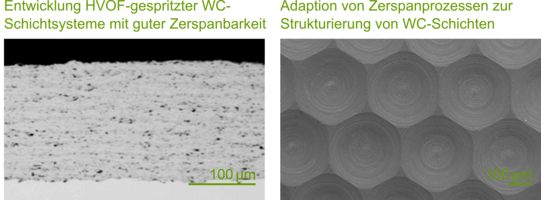