Entwicklung eines prozesskettenverkürzenden Herstellungsverfahrens für die Fertigung von Druckgussformeinsätzen auf Basis einer simulationsgestützten Methodik und ressourceneffizienten Recyclingansätzen
Die Fertigung von Kokillen, Druck- und Spritzgussformen sowie von Schmiedegesenken zeichnet sich durch hohe Anforderungen an die Qualität der bearbeiteten Oberflächen von Werkstücken aus schwer zerspanbaren Werkstoffen aus. Deshalb kommen mehrstufige Prozessketten zum Einsatz. Einer Fräsbearbeitung folgen meist Erodierprozesse zur Fertigung besonders tiefer Kavitäten, welche im Fräsprozess noch nicht prozesssicher fertigbar sind, und häufig manuelle Polierarbeiten erfordern, um die gewünschte Oberflächenqualität zu erzielen. Das Fräsen ist im Kontext der Formgebung von zentraler Bedeutung, da die höchsten möglichen Materialabtragsraten erreichbar sind. Bei der spanen-den Bearbeitung gehärteter, schwer zerspanbarer Werkzeugstähle, welche sehr häufig im Werkzeug- und Formenbau zu bearbeiten sind, können hohe Prozesskräfte wirken. Da zur Fräsbearbeitung tiefer Kavitäten langauskragende und damit nachgiebige Fräswerkzeuge eingesetzt werden müssen, ist das Risiko des Auftretens dynamischer Störeffekte, wie dem regenerativen Rattern, vergleichsweise hoch. Daher wird in vielen Fällen auf weniger produktive Erodieroperationen ausgewichen, wobei die sequenzielle, teilweise unternehmensübergreifende Verkettung unterschiedlicher Prozessarten zu hohen Nebenzeitanteilen führt, weshalb die Bearbeitung eines Auftrags nach Rohteillieferung bis zu 20 Tage in Anspruch nehmen kann. Zusätzlich führt die Verkettung unterschiedlicher Bearbeitungsprozesse zu erheblich höheren logistischen und administrativen Kosten. Das notwendige Einmessen des Bauteils stellt einen zeitaufwändigen Arbeitsvorgang und eine zusätzliche Fehlerquelle dar. Die im Erodierprozess erzeugten Oberflächen müssten stets z. B. in einem Polier-prozess nachbearbeitet werden und weisen in der Regel ungünstige Eigenschaften hinsichtlich der Oberflächenrandzone auf, wie z. B. Zugeigenspannungen.
Durch die Entwicklung eines neuen Herstellungsverfahrens unter Einsatz simulations-gestützter Prozessoptimierungsmethoden soll im vorliegenden Projekt eine „Expressfertigung“ von Druckgussformeinsätzen realisiert werden. Durch den konsequenten Einsatz von Simulationstechniken sollen eine erhebliche Verkürzung der Prozessketten sowie reduzierte Planungs- und Prozesslaufzeiten ermöglicht werden. Eine mit dem neuen Herstellungsverfahren erreichbare Beschleunigung der Angebotserstellung und Lieferzeit kann somit einen Wettbewerbsvorteil sichern. In diesem Kontext spielt die Ressourceneffizienz in multipler Hinsicht eine zentrale Rolle: Die Beschleunigung von Produktionsprozessen bindet Ressourcen wie Mitarbeiter, Maschinen, Werkzeuge und Lagerfläche für eine kürzere Zeit. Die Kunden müssen Ersatzteile nur in geringerem Umfang vorhalten und bei Einführung einer Methode zum Recycling von Formwerk-zeugen durch Aufbereitung lassen sich Rohstoffressourcen und Vorbearbeitungsschritte einsparen.
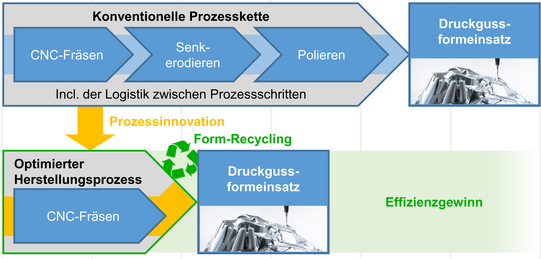