Simulationsbasierte Auslegung von Hochleistungs-Innenrundschleifprozessen
Lange Kornkontaktzeiten, komplexe Eingriffsbedingungen und die erschwerte Kühlschmierstoffversorgung aufgrund der geometrischen Randbedingungen stellen eine große Herausforderung bei der Prozessauslegung des Innenrundlängs- und Innenrundeinstechschleifens dar. Eine Alternative ist das Innenrundschälschleifen, das sich durch eine hohe Flexibilität und Wirtschaftlichkeit auszeichnet.
Verwendet werden dabei schmale, galvanisch belegte CBN-Schleifscheiben, die in zwei Bereiche, einer konischen Schrupp- und einer zylindrischen Schlichtzone, unterteilt sind. Diese werden bei der Innenrundbearbeitung von gehärteten Stählen eingesetzt, da aufgrund des großen Spanraumes und der aggressiven Schleifscheibentopographie eine hohe Produktivität gewährleistet wird. Eine deutliche Steigerung des Zeitspanvolumens kann durch die Hochgeschwindigkeitsbearbeitung realisiert werden. Mit einer Einsatzvorbereitung der Schlichtzone der Schleifscheibe können gleichzeitig gemittelte Rautiefen von Rz ≈ 2 µm am Bauteil gewährleistet werden. Aufgrund der im Vergleich zu anderen Schleifprozessen kleinen Kontaktzone sind die Prozesskräfte gering. Die aus dem Prozess resultierende Wärme wird lokal konzentriert in das Bauteil eingebracht. Durch die hohe Wärmebelastung des Bauteils können thermisch bedingte Bearbeitungsfehler, wie z. B. durch die thermische Ausdehnung bedingte Maßabweichungen und Randzonenveränderungen entstehen, die sich auf die Betriebseigenschaften des Bauteils negativ auswirken. Zusätzlich negativ beeinflusst werden kann die Fertigungsgenauigkeit des Werkstücks durch eine elastische Deformation in Folge der Werkstückeinspannung sowie einer Nachgiebigkeit von Werkstück- und Werkzeugspindeln bei der Bearbeitung. Um prozesssicher Bauteile mit hohen Fertigungsgenauigkeiten zu realisieren, ist es entscheidend, diese Einflussfaktoren zu kennen und im Vorfeld zu vermeiden.
Im Rahmen eines grundlegenden Kooperationsprojekts wurde ein mehrskaliges Simulationssystem entwickelt, das die thermomechanischen Belastungen des Hochleistungs-Innenrundlängsschleifprozesses und deren Auswirkungen auf Fertigungsfehler auf mehreren Betrachtungsebenen modelliert, siehe Abbildung. Aus diesem Modell abgeleitete Kompensationsmaßnahmen erwiesen sich als äußerst zielführend, sodass der Fertigungsfehler entlang der Bohrungstiefe um die Hälfte reduziert werden konnte. Die Ausnahme bildete hierbei der Auslaufbereich des Werkstückes, bei dem bedingt durch die Nachgiebigkeiten der Spindeln eine relativ große Maßabweichung verbleibt.
Das darauf aufbauende Erkenntnistransfer-Projekt verfolgt das Ziel, das entwickelte, mehrskalige Simulationssystem zu erweitern, um es in einer ersten prototypischen Lösung in der industriellen Praxis einzusetzen. In diesem Rahmen werden die Spindelnachgiebigkeiten und der Einzelkornverschleiß in den Komponenten des Systems detailliert modelliert, um alle relevanten Modellierungsaspekte beim Innenrundlängsschleifen berücksichtigen zu können. Durch eine enge Kooperation mit den Anwendungspartnern werden industrierelevante Anforderungen an eine simulationsbasierte Werkzeug- und Prozessauslegung definiert. Durch die Anwendung des mehrskaligen Simulationssystems werden die CBN-Schleifscheiben optimal ausgelegt, im Vorfeld bereits NC-Kompensationsbahnen simulationsbasiert ermittelt und experimentell validiert. Hierdurch wird die Einsatzeignung des Simulationssystems in der industriellen Praxis herausgestellt, um umfangreiche Verschleißuntersuchungen und Einfahrprozesse bei der Veränderungen der Prozessrahmenbedingungen bereits im Vorfeld simulationsbasiert nachbilden zu können. Das gekoppelte Simulationssystem kann in der Prozessauslegung und -optimierung eingesetzt werden, um potentielle Bearbeitungsfehler schon im Vorfeld zu vermeiden.
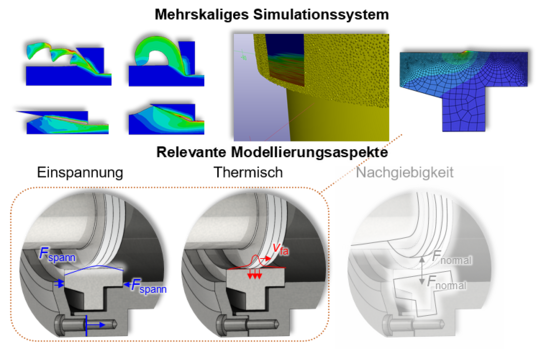