Process and Tool Development for Micromilling of Cemented Carbides
Due to their high hardness combined with good ductility, WC-Co-based solid carbides represent an essential property profile for the manufacturing of highly stressed tool systems in the field of modern tool and mould making. The bending and fracture strength of high speed steels limits their use in tribologically highly loaded processes due to the resulting short tool life. For this reason, cemented carbides are of major relevance in the field of forming and injection moulding technologies. However, the structure of the composite material consisting of tungsten carbides and a ductile binder-phase presents a major challenge for the machining technologies used. Although established processes such as electric discharge machining (EDM) and laser ablation offer the possibility of machining these materials in general, high thermal loads negatively influence the surface and sub-surface conditions. This can lead to impaired surface integrity, which in turn affects production performance by negatively influencing fatigue and wear behaviour. Complex downstream processes and long process chains are required to overcome this impairment. Furthermore, conventional macromachining processes, such as grinding, are limited by the lateral dimensions of the tools as well as limited accessibility of the machining area. This is particularly important when machining filigree shape elements. Taking into account the current trend of miniaturisation, the field of machining technology offers only insufficient possibilities for the processing of tungsten carbide. A stable and efficient process for machining cemented carbides with micro milling tools could provide an alternative to established processes that combines shaping and surface conditioning. In this respect, micromachining, e.g., micromilling, offers great potential regarding the achievable surface roughness as well as sub-surface condition and resulting residual stress state. However, the machining of sintered cemented carbides has not been sufficiently researched to achieve a profound process design. Regarding the machinability and achievable production quality, there is still no comprehensive understanding of the influence of the specification of the cemented carbide, such as grain size and binder content. In addition, the wear behaviour during micromilling has not yet been fundamentally investigated. Considering the economic performance of these processes, this offers great potential in terms of tool lifetime as well as tool optimisation. In this context, cutting edge preparations, current developments in the field of PVD coating technology and the synergy effects of both approaches offer promising opportunities.
The overall objective of the research project is to identify the fundamental mechanisms and interrelationships in the micromachining of solid carbides with varying binder content and grain size. The micromilling of this class of materials can be made accessible by obtaining a basic understanding of advantageous ranges of cutting parameters and technological limits with PCD and CVD coated tools. Furthermore, this investigation focuses on the adjustment of a ductile chip removal process depending on the material specification in order to be able to ensure a high degree of manufacturing quality. In addition to process-related fundamentals, the identification of dominating wear mechanisms and the occurring process specific thermo-mechanical load spectrum in micromilling of carbide are in the centre focus. Based on this, a load-specific conditioning and preparation of the cutting edge is considered in order to increase the wear resistance and therefore the tool life. The application of mono- and multilayer PVD thin-film coatings are still completely untapped. However, nitride or boride hard material coating offers great potential for this manufacturing field. This interdisciplinary research project is strengthened by the cooperation with the Institute of Materials Engineering (LWT).
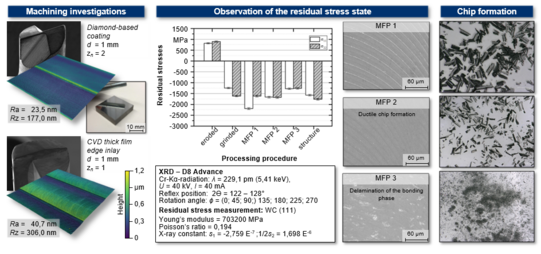