Effects and interactions for interface and cutting-edge conditioning in hard mircomachining
Micromilling processes offer important advantages in hard machining, e.g., for the machining of hardened high-speed steels. Thus, superior surface qualities can be achieved with higher removal rates and less thermal impact on the peripheral zone compared to alternative microsystem processes such as laser ablation and erosion. In addition to the achievable manufacturing quality, this results in significant advantages with regard to the technical properties of the workpieces. Applications of micromachining processes are increasingly found in the field of tool and mould manufacturing. In this sector the production of functional surface structures or filigree secondary mould elements can be achieved by micromilling without the need for post-processing, which explains the increasing importance of the process. The reason for this can be attributed to the mechanical and geometrically determined engagement of the tool and the related controllability of the material removal. However, these advantages are offset by the limited lifetime of the filigree tools (d ≤ 1 mm), which restricts the potential of the manufacturing process. The reason for this is the high process stress during the hard machining, which can be attributed to the thermomechanical load collective. The wear on the tool leads to unfavourable engagement situations or sudden tool failure due to changes in the shape of the cutting edge. This results in poor component quality and ultimately rejects in production. In tool and mould manufacturing, this is associated with considerable costs for the manufacturing companies due to the high complexity of the components, the materials used and the length of the process chain. This results in the inevitable need to increase tool life and thus the stability of the production process.
Among other things, the mechanical and chemical properties of the coating and its adhesion are decisive for the tool life of solid carbide tools. These factors highly depend not only on the coating process itself, but also on the pre-machining strategy and conditioning of the tool. For instance, the shape and condition of the cutting edge has a significant influence on the coatability of the tools’ cutting edges. If the processes are not sufficiently adapted, weak points on the tools can arise in the coating process, causing germination points for wear in the machining process. However, these effects and interactions have not yet been scientifically conclusively clarified. Especially under the requirements of hard machining combined with the filigree tools in micromachining there still is a considerable need for research. This especially addresses the interactions of the process chain for tool optimization, consisting of cutting-edge preparation, coating pre-treatment, coating and post-processing of the coating. The overall objective of the project therefore is to understand the fundamentals of micromachining as a function of cutting-edge shape and interface modification as well as their interactions with novel nitridic hard material coatings for hard machining. Based on these, finding an improvement of the efficiency of the hard machining process with geometrically defined cutting edges can be carried out. This objective is based on the hypothesis that more oxidation and abrasion resistant coating systems have a positive influence on the tool performance with regard to wear, tool life and achievable surface quality. The adhesion of the coating systems is enhanced by increasing the ionization in the DC/HiPIMS coating process and by means of a suitable pre-treatment in the form of a specific adjustment of the cutting-edge geometry and the adjacent functional surfaces.
The findings from the project contribute to a more intensive understanding of the interaction of the individual processes and allow the utilization of the performance of modern HiPIMS layer systems. Due to the basic character of the investigations carried out, a transferability to other machining processes is ensured, so that they can provide the basis for further process optimizations.
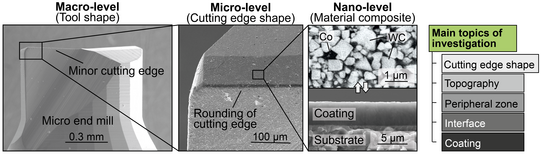