Process Parameter Correlated Characterisation of the Corrosion Fatigue Behaviour of Post-Treated ZnAl-Coated Arc-Sprayed Systems
Thermally sprayed protective coatings are applied onto many mechanically stressed components such as support structures, shafts, turbine blades, and heat exchangers. In many cases, in addition to the static or dynamic loading, a superimposition with corrosion processes, e.g., high temperature corrosion or electrochemical corrosion, occurs. Within this context, it does not matter if the coating was designed for corrosion protection or wear protection, since the stresses can occur in either case.
The corrosion behaviour of arc-sprayed ZnAl-based coating systems has already been studied extensively. However, the investigation methods which were used are predominantly based on simple corrosion tests, such as salt spray tests or electrochemical corrosion measurements. With regard to the technical applications of ZnAl-based coating systems in the field of surface technology, the chemo-mechanically coupled load spectrum is considered only to a limited extent. In most cases, the mechanical loads of the components or of the coatings, which occur in real applications, including the corrosive environmental conditions, are not taken into consideration. Yet, it is to be expected that a mechanical load significantly changes the service life (fatigue) and the corrosion behaviour of the layer-substrate-system. Corrosion mechanisms such as stress or vibration crack corrosion will be of high interest. Additionally, a different electrochemical potential of the layer and the substrate can lead to accelerated corrosion. Scientifically, the extent to which the coating influences the occurring corrosion mechanisms, as well as the kind of layer-substrate interaction that takes place, are of interest.
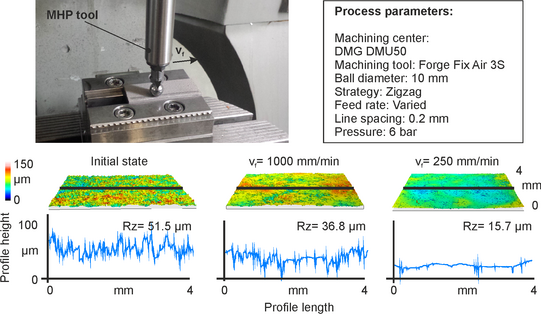
In order to investigate these questions, in-situ corrosion fatigue tests with different polarisations are planned. For this, different ZnAl-based layer systems, varying in hardness, lamellar structure and porosity, will be developed and analysed. Furthermore, it will be investigated to which extent machine hammer peening (MHP) as a post-treatment influences the morphology and corrosion fatigue behaviour of the coating system.