Biologized Clamping Technology (BioClamp)
The increasing industrial demand for filigree components, e.g. made of difficult-to-machine materials, requires suitable workpiece clamping devices that enable precise and reliable machining under the specific challenges of deformation-free clamping. As a result of the often unfavourable clamping forces, conventional clamping systems can cause critical shape deviation and damage to thin-walled components. Approaches for the further development of conventional clamping devices, which are based on a bionically motivated surface functionalization, show considerable potential for reducing the required proportion of the normal clamping forces by maximizing the frictional and holding forces. The tick species Ixodes ricinus serves as a model here, which can convince with combination gripping tools consisting of robust claws and flexible pads through relatively high holding forces.
An essential objective is the development of a clamping device equipped with functionalized clamping surfaces for process-reliable workpiece clamping of deformation-sensitive components. For this purpose, novel approaches on the micro- and nano-structural level are to be combined in order to develop a biologized clamping contact surface that can realize a more efficient force transmission by means of an increased frictional connection between workpiece and clamping element. In addition, relevant characteristics of the resulting clamping and machining process are to be measured by means of sensor integration in order to increase process reliability and evaluate the effectiveness of the developed workpiece clamping surfaces.
To achieve these objectives, a representative reference error in the clamping of a deformation-sensitive component is to be defined using a classical clamping device. In the further course, the technological expertise of the Institute of Machining Technology (ISF) and the Fraunhofer Institute for Material and Beam Technology (IWS) in the field of surface structuring as well as coating by means of PVD carbon coating systems will be focused on the clamping context as well as further developed. Selected surface modifications are tested in a test rig with regard to their holding force and then combined to form a hierarchically functional surface system. The resulting clamping elements with optimized frictional locking in the contact zone are validated in coordination with the industrial patron ROEMHELD Group on a demonstrator workpiece clamping system for load-adapted clamping. In addition, the clamping system will be functionally extended with suitable pressure and structure-borne sound sensors to enable an evaluation of the clamping process based on clamping pressure and contact situation with minimized component deformation.
Finally, the demonstrator system of the research project is to be transferred to a prototype clamping system in the industrial production environment in coordination with innovative end customers from the plastics processing, automotive and aerospace industries. After the evaluation of technological and economic conditions, the transfer to series products is an essential step to strengthen the performance of the product range of SMEs today and for future trends in the field of manufacturing, as well as for the use of new materials. The contribution to the productivity of machining processes is complemented by the reduction of scrap parts, which increases the efficiency of material and energy utilization as well as the economic and ecological competitiveness of SMEs in the national and international market environment.
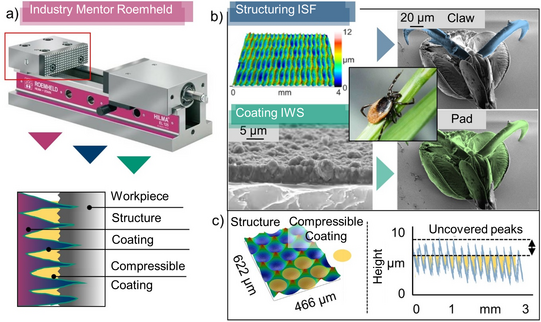