Flexible internal turning at any machining depth
A major part of production technology is realized with machining. The complexity of many components is increasing across all industries, as are the demands placed on them. For this, the workpieces must have diverse and precisely manufactured contours. While extensive possibilities for mechanical machining are available in the field of external machining, these possibilities are significantly reduced in the case of internal machining due to the difficult accessibility and the limited installation space. Therefore, internal machining, especially for smaller components, is limited to cylindrical bores and internal contouring at shallow depths. For internal turning, the achievable bore length-to-bore diameter ratio (l/D ratio) with already vibration-damped turning tools is l/D < 7. In contrast, bottle boring tool systems allow higher l/D ratios, but only from a larger machining diameter due to the complex mechanical structure. This limits the potential for full-scale machining of a component with regard to the following points:
- Higher component weight, as material in greater component depths cannot be removed in a suitable manner
- Lower component load capacity, as no load-adapted inner contour can be produced and thus shorter product life and higher risk of component failure
- Reduced functionality, as there is no possibility of introducing functionally relevant contours in greater component depths.
The above-mentioned deficits of the status quo of internal machining motivate the development of a new machining process for metal-cutting production, with which the internal contouring of small component diameters in the range of D = 10...40 mm is also possible at large machining depths. This addresses the mentioned deficits and completes the existing possibilities for internal machining for the previously unattainable diameter ranges at almost any machining depths through an l/D ratio of up to 100. In this way, a more consistent lightweight construction can be pursued and safer, more functional and more resilient products can be manufactured. The system to be developed is to be used by SMEs on existing machine tools, so that technological advances and unique selling points can result from new or improved existing products.
The project is being implemented in cooperation with two SMEs and includes a holistic approach to the development of the tool system. Through this, the mechanical, mechatronic and simulative development of the system will take place over the duration of the project, as well as application tests on various machine tools. The project will be completed with the first use of the new machining process by a manufacturer in an industrial production environment.
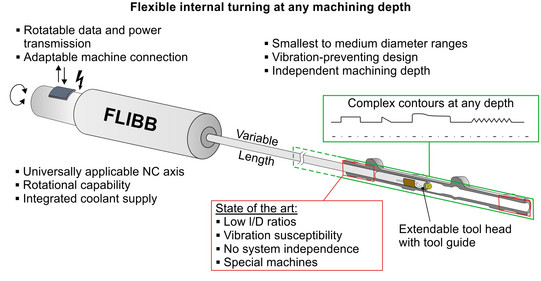