Efficient Modelling of Chip Formation in Orthogonal Cutting Based on Isogeometric Analysis and Modern Methods for Material Characterisation
This project, which is funded by the German Research Foundation (DFG), considers the numerical simulation of chip formation and its potential to predict process variables for cutting processes. Also available in commercial software, the numerical simulation of chip formation based on the Finite Element (FE) method is a commonly used approach to predict the complex thermo-mechanical effects in cutting, in particular in the vicinity of the cutting edge. However, the state of the art shows limitations, i.e. on the one hand the actual chip formation simulations only permit the representation of very short process sequences and on the other hand their underlying models are of limited validity, in particular in terms of the quantitative prediction of process values such as forces, stresses, strains, temperatures, and chip shapes. These limitations result at least partially from insufficient material and friction models. However, clear evidence exists that the utilised FE meshes (refinement, element type, element deformation and orientation) have a strong influence not only on the accuracy of the numerical result, but also on the general phenomena that can be captured, especially the development of shear bands. These dependencies are intended to be resolved by the use of modern numerical methods, namely Isogeometric Analysis (IGA) and space-time finite elements.
The specific scientific aim of the project is to develop a modern numerical analysis tool for chip formation based on IGA and the Deforming-Spatial-Domain/Stabilized Space-Time (DSD/SST) method, which is already established in computational fluid dynamics. The new tool is to be assessed in terms of efficiency and accuracy, in particular regarding effects in the primary and secondary shear zone, but also the workpiece surface zone. The developed modelling approach has to be supported by modern methods of material characterisation. For this purpose, yield stress characterisations for the materials C45 and Ti6Al4V were performed using a Split-Hopkinson-Pressure-Bar (SHPB) available at ISF. Based on the results, phenomenological material models could be parameterised, which describe the dependence on strain, strain rate and temperature. In addition, by using an investigational approach for friction characterisation developed especially for machining, it was possible to develop velocity dependent models for the friction coefficient according to Coulomb. Compared to the use of constant values, these extended friction formulations allow an improved description of the contact in the secondary shear zones.
On the methodological side, a better understanding of the behaviour of IGA can be achieved when modelling dynamic contact problems with thermodynamically coupled material equations. Especially the significant reduction of numerical errors, which are induced through remeshing steps, are expected to lead to an increase in numerical accuracy. This constitutes an important step for chip formation simulation and will immediately improve its applicability. For the validation of the simulations, cutting experiments were conducted.
A dynamic cylinder contraction comparable to the Split-Hopkinson-Pressure-Bar test principle served as a first application for the newly developed IGA method. The material model parameters were derived from an experimental flow stress characterization. A comparison with FE simulations in a commercial system showed a good agreement of the predicted deformation behaviour.
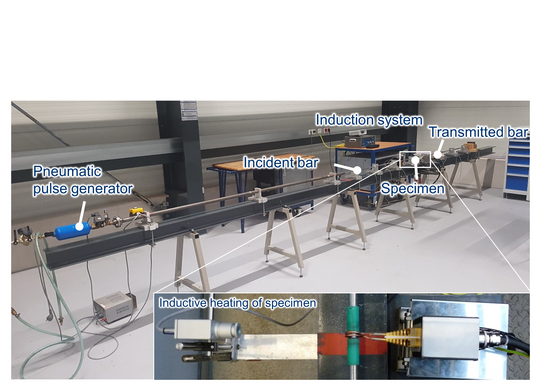