Investigations on the Influence of Machining and Sulphur Content on the Fatigue Strength of the Quenched and Tempered Steel 42CrMo4+QT
The fatigue behaviour of components made of quenched and tempered steel alloys is of elementary importance, especially in the automotive industry. To a great extent, the components fatigue strength is influenced by its surface integrity properties. For machined components, the generated surface is often exposed to the highest thermo-mechanical loads, which can influence the subsurface microstructure and hardness as well as the residual stress state. In this research project, on the example of single-lip deep hole drilling, the promising approach of a function-oriented process design is pursued, which includes the analysis and utilisation of the occurring thermomechanical effects in order to increase the fatigue behaviour of deep drilled components. In order to achieve this objective, a process strategy is to be developed with which the surface and subsurface properties generated during single-lip deep hole drilling can be influenced specifically. This will allow to adjust the required surface integrity already during deep hole drilling and thus to save cost-intensive downstream surface treatment processes, such as a hydraulic autofrettage process. The material used is the quenched and tempered steel AISI 4140 (42CrMo4+QT), which is widely used in industrial applications, especially for components that are subject to high mechanical or cyclical loads. Different alloy variants of the quenched and tempered steel with varying sulphur content are investigated, which affects the number and size of the manganese sulphides contained in the microstructure.
Within the project, experimental and fundamental studies on manufacturing technology and material behaviour are combined and further developments of innovative methods for materials testing are carried out. In the first part of the project, the correlation between the process parameters, the associated thermomechanical effects on the bore wall, the achieved surface integrity properties and the resulting fatigue strength will be investigated experimentally. In addition to established methods for the characterisation of the obtained subsurface properties, innovative non-destructive methods such as the Barkhausen Noise Analysis (BNA) will be applied.
In addition to the mechanical effects, the generated surface integrity is affected by thermal effects acting on the bore wall during single-lip deep hole drilling, which are largely unexplored. Therefore, in the current project phase, a test set-up is being developed and applied to enable an in-process temperature measurement during deep-hole drilling. With this test set-up, it is possible to gain information about the maximum temperatures in the subsurface of the bore wall as well as directly at the cutting edge of the single-lip drill. The results of the experimental investigations will be used in a subsequent step for the development and validation of a numerical model, which is able to represent the correlations between the process parameters and the fatigue strength of the deep drilled specimens. The research activities aim to enable the dynamic strength of the components to be predicted for different combinations of process parameters and to increase it by specific adaptions.
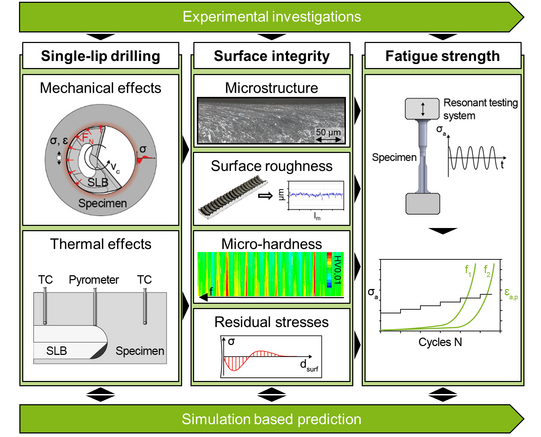