Holistic Development and Characterisation of an Efficient Manufacturing of Detachable Joints for Aluminium and Magnesium Lightweight Materials
Metallic lightweight construction materials are used, for example, to increase efficiency and reduce emissions in many areas of the aerospace industry. Various welding, soldering, adhesive or screw connections are used to join the components. Flow drilling in combination with subsequent thread production for metallic lightweight profiles offers the possibility of producing an internal thread with a greater usable thread depth by locally expanding the material. Compared to conventional joining methods, the introduction of threads at the front end also offers significant potential for increasing efficiency in industrial production.
Within the framework of this research project, the status of the flow drilling process developed so far for the aluminium and magnesium alloys AlSi10Mg and AZ91 is to be extended with regard to technological and economic aspects. Related challenges, especially in the machining of the magnesium alloy AZ91, are to be overcome by the preceding insertion of a conventionally produced pilot hole. This is followed by the flow forming process, which produces the core bore necessary for thread forming. In contrast to thread machining, this process offers the advantage that the forming process results in work hardening of the material in the edge zone of the bore. On the basis of research results already obtained, the front-face flow drilling process is further being developed with regard to innovative tool concepts and other optimisation approaches. Selected process parameters, such as the initial tool temperature or the tool coating, are varied within the scope of the experimental investigations and evaluated comparatively with the help of the mechanical characterisation methods to be carried out by the Department of Materials Testing Technology. Due to the iterative character of the research project, the results are validated in this way. By transferring the results to industrial production, a resource-saving and efficient processing should be possible.
The research project aims at the holistic further development and characterisation of the face side flow drilling with subsequent threading of aluminium and magnesium alloys. In addition to further optimisation of the machining strategy, which will be advanced by means of the findings from practical tests, technological challenges are to be overcome by applying different tool concepts. The process-related geometric or microstructural properties of the internal threads are related to the mechanical properties, resulting in a structure-based analysis of the damage mechanisms, the understanding of which is absolutely necessary for the design of optimal process conditions.
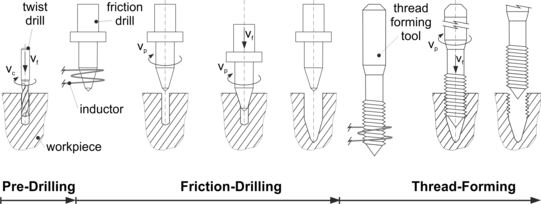