Restriction of the Chip Thickness Deviations for Stabilising the Chip Formation of High Strength Metals
Chattering of the manufacturing system consisting of tool, workpiece and machine are a major challenge in machining of lightweight components. In particular, the machining of titanium alloys, which have high strength combined with high ductility and low thermal conductivity, is problematic. A significant influence on the process is the characteristic serrated chip formation, since the formation of serrated chips is related to a periodic excitation of the tool. This leads to a reduction of the surface quality and the tool life as well as a significant shortening of the fatigue life of machine components. In order to counteract this problem, forcing a continuous flow chip formation is a promising approach.
The aim of this research project, which is funded by the German Research Foundation (DFG), is to use a device that specifically influences the form of the chip. By means of a continuous chip formation, the generation of vibrations can be suppressed and thus absorption techniques like damping become obsolete. The formation of continuous chips can be induced by an additional element during chip formation. For this purpose, the additional element, the constraint, is positioned on the free surface of the workpiece at the end of the primary shear zone (see Fig.). The constraint leads to a stress state with high hydrostatic pressure in the shear zone, which prevents material failure. However, the use of the constraint results in increased mechanical tool loads, which can lead to early tool failure and damage to machine components. Therefore, it is necessary to find a balance between the influence of the chip formation and the occurring mechanical loads. These aspects have to be taken into account by choosing a suitable geometric shape and a suitable positioning of the constraint. For this purpose, a series of experimental investigations are carried out to analyse the formation of the chips using high-speed videography. In addition, the failure mechanisms in the area of the shear bands are investigated by means of detailed analyses of the chips at different process parameters. Subsequently, the free chip formation is simulated in an FE-model and after successful modelling a suitable geometry as well as positioning of the constraint is worked out simulatively. Finally, the simulatively determined optimum with regard to design and positioning of the constraint is validated in experimental investigations. In order to avoid mechanical overload, a second design approach is to be pursued in which the constraint is not fixed in position, but is impinged with a spring. This construction is able to prevent an overload of the tool as well as suppressing the serrated chip formation. The workpiece material used in this research project is the titanium alloy Ti6Al4V, which has a distinctive tendency to serrated chip formation.
First experiments have already shown the feasibility of this concept. Without prior analysis of the geometric shape and exact positioning of the constraint, chip formation analyses were carried out on a specially designed machine with a carbide insert turned by 90° as a constraint. The titanium alloy Ti6246 was used as workpiece material. During the execution of orthogonal cutting tests, a strong serration of the chip was observed for free chip formation. By positioning the constraint in the area of the primary shear zone on the free workpiece surface, the development of shear bands and thus the serration of the chip could already be successfully suppressed.
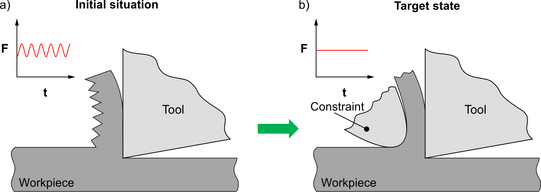