Modelling of the Cooling Lubricant Distribution during Single-Lip Deep Drilling with Consideration of Chip Transport by Means of CFD and SPH/DEM Simulation for Tool and Process Optimisation
In contrast to twist drill deep hole drilling, single-lip deep hole drilling is a process in which the contact of the guide pads with the borehole wall contributes to a smoother surface and a very high borehole quality. Particularly when machining difficult-to-machine materials, such as nickel-based alloys, the tools are subject to immense thermomechanical loads, which make an optimum supply of cooling lubricant to the cutting edges of the tool indispensable. However, the detection and reduction of the tribological stresses that underlie single-lip deep drilling processes pose a major challenge, as the contact zone is experimentally inaccessible and cannot be reached with measuring systems. The aim of this project therefore is an adequate modelling of the process by combining suitable simulation approaches to model the dependence of the optimal cooling lubricant supply on the pressure conditions and the tool shape with a simultaneous mapping of the transient chip removal. The analysis of different tool design variations with regard to an efficient coolant supply leads to the development of tools with lower tool wear and increases the process reliability for single-lip deep hole drilling.
In order to investigate the above-mentioned aspects and correlations and to optimise the tool based on the coolant flow simulation, it is necessary to combine or couple different simulation methods. A simulation approach which includes the Finite Element Method (FEM), Computational Fluid Dynamics (CFD), Smoothed Particle Hydrodynamics (SPH) and the Discrete Element Method (DEM) will be developed. The grid-based CFD simulation describes the coolant flow with all relevant boundary conditions, such as fluid properties, mass and volume flow, friction and turbulence. The grid-free SPH/DEM method simulates the transport of the chips. This enables detailed flow analyses at discrete points in time with regard to the coolant distribution at the cutting edges of the tool, the consideration of the position of the respective chips, as well as the calculation of precise pressure distributions. Thus, a targeted optimisation of the tool design is made possible.
The experimental investigations of drilling Inconel 718 are carried out with a solid carbide single-lip deep hole drill with a diameter of d = 2 mm. The combination of material, tool design and dimensions was chosen because of its high relevance for the production of heavy-duty bores in various areas such as aerospace. The results serve as input and validation data for the simulations and for the optimisation of the tools. A visual recording of the chip formation is carried out with high-speed microscopy, whereas the mechanical tool loads are analysed with established measuring methods. The concluding optimisation is performed with the optimisation tool (OptiSLang) by bi-directionally coupling the computer-aided design (CAD) and CFD simulation environment (ANSYS DesignModeler and ANSYS CFX/-FLUENT) and integrating it into the higher-level simulation environment (ANSYS Workbench).
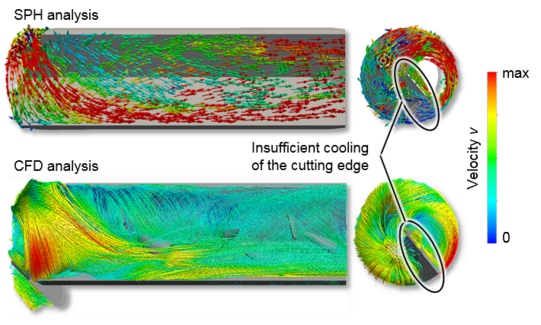