Development and implementation of a concept for the use of a low temperature emulsion in the drilling of Inconel 718
Demanding, heat-resistant materials are a core element in the production of highly resilient, high-quality components. These materials include nickel-based alloys, of which Inconel 718 in particular is used in applications such as aerospace. Nickel-base alloys are characterized by their high-temperature strength, creep resistance and resistance to corrosion and chemical influences. These properties result in special challenges during the machining, especially drilling, of these usually cost-intensive, safety-critical components. Due to their low thermal conductivity, the alloys favour an increased thermal energy flow to the cutting material. In order to prevent intensive tool wear of the solid carbide tools, which are often used for drilling Inconel 718, and the subsequent reduction of the bore quality, the temperatures during machining must be kept low. The difficult accessibility of the working area during drilling limits the possibilities of process cooling and therefore the cutting speeds that can be achieved.
In order to increase the cutting speed and hence the process productivity, the research project aims to modify the cooling lubricant concept. The advantages of the existing concepts, which include internal high-pressure cooling with emulsion and cryogenic cooling with liquid nitrogen or carbon dioxide, are to be combined in the development of a low-temperature emulsion. The new emulsion combines high heat capacity and conductivity with effective process cooling and improved heat removal. This should enable higher cutting speeds, a longer tool life and improved workpiece surfaces. In the research project, an emulsion that can be cooled down to T = -20°C and an appertaining coolant system, which includes an isolated tank and a cooling unit, are being developed. In addition, the machine tool and its periphery must be adapted to the new operating conditions. The operational capability of the new system will then be comprehensively technologically analysed and compared with a reference cooling lubricant. For this purpose, tests with different cutting speeds and cooling lubricant supply temperatures will be realized on a machining centre adapted to the project conditions. The aspects to be investigated include tool wear, process forces, chip formation, bore quality and accuracy, cutting edge and workpiece temperatures and the bore edge zone integrity.
If the research project is successfully completed, higher profitability, process reliability and resource efficiency can be achieved in the drilling of nickel-based alloys such as Inconel 718. The results are of particular relevance for manufacturers of cooling lubricants, tools, machines and periphery as well as the actual production users and can contribute to the establishment of the extended use of emulsion.
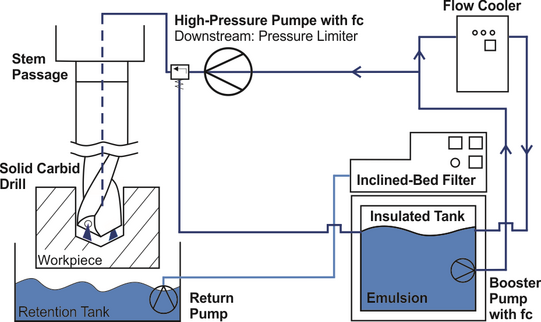