Simulation-Based Development and Experimental Validation of Tool-Integrated Rotary Particle Dampers
Depending on the given process conditions, milling of forming tool components made of hot-work tool steel can be associated with pronounced regenerative chatter vibrations. Among others, increased tool wear and significant damage of the component surfaces can thereby occur. Basic tests on milling with particle-damped HSK63 tool holders have already shown that the use of rotary particle dampers (RPD) is a suitable approach for reducing tool vibrations. This enables process-stable material removal even with usually vibration-critical parameters. Based on these results, this research project funded by the German Research Foundation (DFG) aims to develop an indexable insert milling cutter with integrated RPD, which will enable increased stability and thus production quality in functional surface machining of large dimensioned tool components. Fundamental simulations of particle dynamics under rotating tool conditions, validated by experimental analogy tests, in cooperation with the Institute of Engineering and Computational Mechanics (ITM) at the University of Stuttgart, allow a systematic conceptual design with significantly reduced time and experimental effort. This combined approach of using well-founded measurement data generated by the analogy experiments to calibrate the particle simulations further enables a fundamental gain in knowledge regarding the particle motion under acting centripetal force and thus a dissipation-efficient system design. In particular, design modifications can be specifically implemented to increase the damping capacity. For example, the application of an internal structure adapted to the particle motion pattern is associated with an increase in the potential contact areas between the particles and the tool holder and consequently increased dissipation of the vibration energy due to inelastic particle impacts. In addition, a macrostructuring of the RPD wall surfaces in accordance with the particle dynamics allows an increased friction dissipation.
An essential part of the systematic RPD design is the analog experimental setup to be developed, which, in conjunction with the specially designed analogy tool, allows a view into the interior of the RPD and thus enables the possibility of additional high-speed videographic recordings of the particle motion during tool rotation. Another key part is the use of periodic boundaries for the simulation setup. This simulation strategy significantly reduces computation times, since only representative parts of the RPD have to be considered in detail in order to systematically transfer the results to the entire simulation area. This procedure has already been successfully applied to translationally excited systems and is to be adapted to the RPD under consideration of the measurement data determined during the analogy experiments. One of the main challenges is to find appropriate subdivisions of the simulation area to obtain valid simulation results. In initial tests with a simplified RDP setup, the feasibility of the intended simulation design could already be fundamentally demonstrated (Figure).
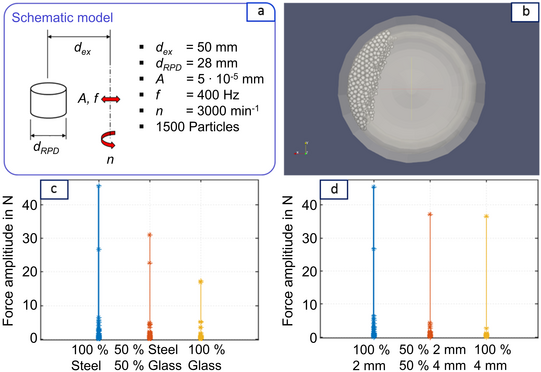