Fundamental investigations on disturbing the regenerative effect in milling processes through the targeted design of tools with asymmetric dynamic properties
Dynamic effects, such as regenerative chatter, often limit the productivity of machining processes. There are five techniques to influence process dynamics and stability: maximizing the stiffness of the production system, maximizing the structural damping of the production system, optimizing the process parameters, maximizing the process damping and disturbing the regenerative effect. Increasing the stiffness or structural damping of a production system is a major challenge in the design of machine tools and is associated with high costs. The optimal design and parameterization of a machining process and optimal use of process damping effects require detailed knowledge of process-specific dynamic properties of the production system, other process variables and extensive expert knowledge in the field of process dynamics. The disturbance of the regenerative effect is largely independent of the framework conditions regarding the production system and process. Thus, this method is particularly interesting in terms of a universally applicable strategy for increasing productivity.
The presented project approach describes a novel method to disturb the development of regenerative chatter vibrations by using milling tools with asymmetric dynamic properties (AsymTools). By a preparation of the tool shank with parallel opposing grooves the dynamic properties, i.e., eigenfrequencies and compliance of milling tools, are modified in dependence of the direction. According to the working hypothesis, milling processes are still subjected to dynamic compliances if AsymTools are used, but the excitation of the vibratory system caused within a previous cut no longer corresponds directly to the eigenfrequency of the tool during a tooth engagement. Thus, self-excited vibrations and the regenerative effect can be disturbed. Within the scope of experimental investigations, an increase of the stability limit and productivity of up to 69 % could be achieved.
The aim of the project initiative described above is to develop methodology for a simulation-based design of AsymTools. To achieve this, the interdependencies between the geometric properties of AsymTools and the process dynamics will first be fundamentally investigated. The effect of a direction-dependent change of the dynamic properties of AsymTools will be analyzed experimentally and by extending and using a geometric physically-based simulation system. For the development of the methodology, the focus is on a compromise between a weakening of the structure in one direction and the differentiation of the direction-dependent natural frequencies under consideration of variant engagement conditions.
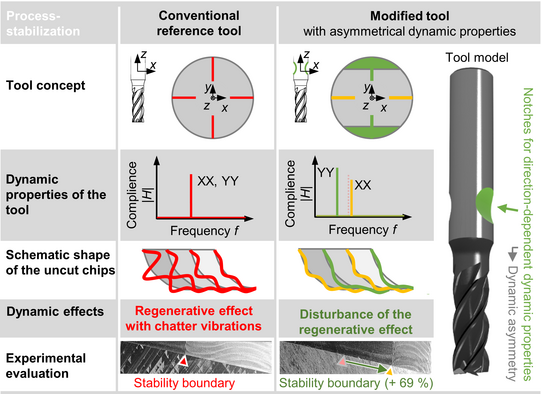
Optional Text