Thin-film sensor systems for guide pads to measure forces, temperatures and wear in cutting processes
Increasing demands on the production of highly loaded components are shifting the focus in machining to the influence of the machining process on the sub-surface zone. Cost-intensive components make sensor-based monitoring and process control increasingly important. The sub-surface condition influenced by induced residual stresses, strain hardening, microstructural changes, crack formation and topography has a significant influence on component behavior under vibrational, tribological and corrosive loads and is currently being investigated in the priority program "Surface Conditioning in Machining Processes" (SPP 2086). Guide-pad-supported processes such as BTA deep hole drilling or single-lip deep hole drilling can achieve highest accuracies and bore hole qualities. The forces acting on the bore hole wall via the guide pads lead to hardening forming processes in the surface-near areas and also improve the bore hole quality by the leveling of feed grooves. As part of the sub-project "Process-integrated measuring and control system for the determination and reliable generation of functionally relevant properties in surface edge zones during BTA deep-hole-drilling", the targeted introduction of sub-surface zone properties is being investigated at the Institute of Machining Technology ISF. The bore hole quality is primarily influenced by the mechanical and thermal loads occurring in the area of the guide pads as well as the wear condition. Using the examples of BTA deep hole drilling and single-lip deep hole drilling, the aim of this trilateral project is to record and utilize the forces and temperatures in the contact zone between the guide pads and the bore hole wall as well as the wear condition of the guide pads by means of a sensory coating with the thin film sensor technology developed at the Fraunhofer Institute for Surface Engineering and Thin Films IST. With the adaptation of the thin film sensor system to the application in machining process and the development of a suitable data transmission from the guide pads via the tool to the machine control system, a prototype of a sensor-based tool system is to be realized at the end of the project. As a passive system, the sensor-based recording of forces, temperatures and wear conditions enables process and tool monitoring to detect critical process conditions and faults, and enables a continuous quality control. With the help of an actively intervening control system, the process can be optimized with suitable approaches (e.g. machine learning) on the basis of the measurement data. Through the cooperation with the companies botek Präzisionsbohrtechnik GmbH, BGTB GmbH and TIBO Tiefbohrtechnik GmbH, the support and influence of the expertise of industrial partners is ensured from the development through the design and production to the application validation.
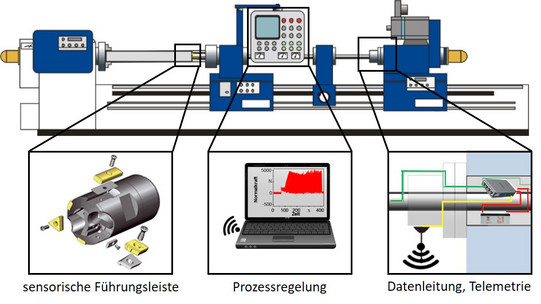