Geometrically Defined Surface Structuring for the Form-Locked Bonding of Thermal Sprayed Coatings
The pre-treatment of substrates for thermal sprayed coatings is conventionally done by abrasive blasting processes using corundum. This step is characterised by a long process time. Moreover, an additional machine is required to realise this kind of pre-treatment.
As an alternative to conventional abrasive blasting, an innovative process combination was developed in this research project (project number 380444554) funded by the German Research Foundation (DFG) at the Institute of Machining Technology (ISF) at TU Dortmund University and at the Institute of Materials Science (IW) at Leibniz University of Hanover, which enables a form-locked bonding of thermally sprayed coatings on substrates. Due to the smart application of knurl milling and deep rolling, it was possible to generate reproducible surface topologies with undercuts in relation to the knurl pitch and the deep rolling strategy as well as the rolling force used. In particular, after generating the required shape of cylindrical workpieces, a periodically repeated tooth topology (knurling) was first machined in the same clamping by knurling milling. This knurling was subsequently rolled in a four-stage mechanical deep rolling process in such way that almost symmetrical undercuts were formed. A further improvement of the coating’s bonding tensile strength could be achieved by an additional hydrostatic deep rolling of the thermal sprayed NiCr8020 coating, positively bonded on the substrate.
The figure shows a selected results' exemplary illustration of tests in which pyramid-shaped cross knurlings with the special pitch of uK = 0.1 mm were rolled and subsequently coated by atmospheric plasma spraying (APS). While the simple process combination without deep rolling the NiCr8020 layer already enabled bonding tensile strength values in the area of conventionally pre-treated substrates, the additionally hydrostatically deep rolled coating showed a 24 % increased layer bonding compared to the reference.
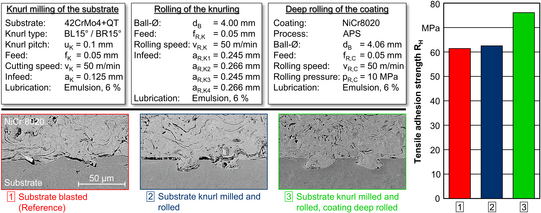
Additionally performed metallographic analysis of the bonding tensile strength specimens tested have shown that the substrates pre-treated with the process combination show a pronounced mixed fracture behaviour with an increased proportion of adhesive layer failure. Due to the surface smoothing associated with rolling the knurling, a reduced adhesion of the coating on the surfaces between the undercuts can be seen. Therefore, further investigations will now aim to improve the layer bonding on the surfaces between the undercuts by additionally roughening them with microfinishing or brushing.
The new process chain can increase the productivity of thermal spraying and enlarge the field of application for thermal sprayed coatings, for instance innovative wear protection coatings for engine applications. Moreover, the smoothed and compacted coatings can be used as functional surfaces as well.