Development of a Novel Chip Formation Model for the Prediction of the Friction-Dependent Chip Breaking Behaviour
The process stability of manufacturing processes is an important factor in the sustainable production of industrial goods. In machining with a geometrically defined cutting edge, process stability depends to a large extent on the chips being removed reliably from the working area. This is a basic requirement, especially for automated production. The main criterion for the removal of chips is their size; consequently, the objective is to achieve chip breaking at a sufficient, reproducible frequency. This poses a challenge when machining ductile and high-purity materials, as their material behaviour allows them to absorb greater deformation without causing chip breakage.
The most common means of generating chip breakage is the use of chip breaker elements on the rake face of the tool, which directs the flow of material in such a way as to favour fracture. Studies have shown that the main disadvantage of chip breaker elements is the limited functional range in terms of materials and cutting values. One of the reasons for this is that the fracture mechanisms and the influences on chip breaking behaviour have not yet been fully researched and, in particular, cannot be adequately represented by models. The planned project is focused on the development of a numerical chip formation model that allows a realistic prediction of the chip breaking process. As illustrated in the figure, the work programme to achieve this objective is presented in collaboration with the Institute of Mechanics (TU Dortmund University).
For this purpose, a Coupled Eulerian-Lagrangian approach is to be used, in which the process of chip breaking can be mapped. The input data regarding the material behaviour as well as the friction behaviour of the tool-workpiece combination are generated using experimental characterisation tests and methods of inverse parameter identification. As a technology application for the novel model, it is planned to investigate the influence of rake face texturing on the chip breaking behaviour of a high-purity quenched and tempered steel. It is hypothesised that the friction-reducing effect of the texture reduces the chip curvature radius, which in turn increases the pre-damage of the material and thus increases the chip fracture tendency. To avoid the inclusion of the texture elements, which have to be very finely meshed, in the simulation-based tool design, friction models are to be developed that map the influence of the textures in order to reduce the computing time. At the end of the project, the developed tools are to be tested for their functionality in experiments. In addition to validating the developed models, these tests will also provide fundamental insights into the chip breaking process, which is to be characterised using modern measurement methods. In addition to dry machining, the influence of flood cooling on chip breaking behaviour will be investigated in both modelling and experiments.
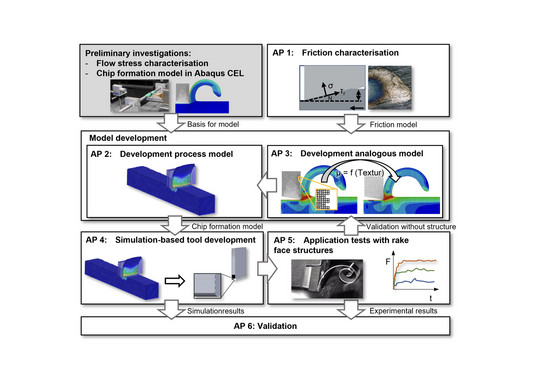