Simulation and optimisation of the coolant flow to reduce thermal tool load during discontinuous drilling of Inconel 718
Drilling of the difficult to machine nickel-base alloy Inconel 718 with its particularly pronounced high-temperature strength is characterized and limited by high tool wear. This is due to the thermomechanical loads on the cutting edges during the machining process. The concept of discontinuous drilling machining as an alternative process strategy is intended to counter this circumstance, so that within the framework of the research project a periodical interruption of the tool engagement is introduced into the drilling process. Thus, a targeted cooling lubricant supply of the highly loaded cutting edges is enabled and consequently a significant reduction of the thermal tool load is achieved. In addition, for discontinuous drilling operations, the cutting interruption favours chip breaking, thus avoiding the formation of long chips which can potentially clog the chip flutes and jam between the bore wall and the tool. At the same time, this process design can be expected to reduce impact on the surface integrity of the workpiece, which is equivalent to increased component quality. Based on these optimisation approaches, the long-term aim is to increase the cutting parameters, which will result in higher productivity.
In order to achieve an optimisation of the drilling of Inconel 718, the development of a deeper process understanding of the thermomechanical load collective is of decisive importance. Due to the poor accessibility of the contact zone and the resulting unfavourable conditions regarding thermal measurements during the drilling process, a complete simulative mapping of the process is moving into the focus of the investigations. At present, however, this cannot be realized or only to a limited extent. Computational Fluid Dynamics (CFD) simulations for modelling coolant flows reflect the local fluid parameters, but do not consider the heat input from the chip formation zone into the fluid. Similarly, in chip formation simulations using Finite Element Method (FEM) technology, the heat transfer from the solid into the fluid is not considered. The central challenge of the research project therefore is to couple the flow simulation with a model of the local temperature distribution in the chip formation zone via a bidirectional combination of CFD and FEM simulations. This enables a complete calculation of the heat transport and thus conclusions to be drawn about the thermal tool and workpiece load. The generated data can be used to predict maximum thermal loads in the process, to identify times of efficient interruptions of the cutting process and thus to carry out an optimized coolant supply of the drilling tools in the discontinuous drilling of Inconel 718. Overall, the desired increase in productivity of the machining process can be achieved with increased tool life.
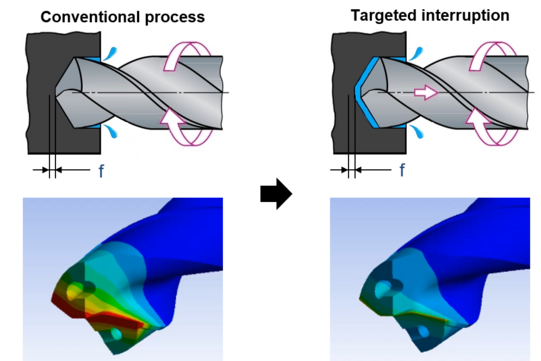