Fundamental Investigations on the Frictional Contact in the Working Zone in Machining Processes
Cutting processes are significantly influenced by frictional events in the contact area of the tool and the workpiece. The working zone is characterised by high deformation rates, contact pressures and temperatures. Therefore, the friction conditions of the chip formation process differ considerably from those covered by established friction tests. In this project, which is funded by the German Research Foundation (DFG), the analysis of friction is supposed to be carried out under the terms of machining conditions with respect to mechanisms and their interactions as well as their interference with process parameters. A special test setup that enables testing conditions similar to those in cutting is used for the investigation. In this test, the workpiece is moved relatively to the tool, so it is plastically deformed. Both objects are made from materials commonly used for machining processes. The sliding velocity, the surface topology and the temperature determine the frictional contact and are investigated in this project. The test setup provides the ability to reach different temperatures at the same sliding velocity, which is an advantage compared to methods like the pin-on-disc-test. Moreover, the influence of the tool‘s surface-topography on the mechanisms which occur in the contact-zone shall be investigated with orthogonal cutting experiments. So far, these experiments have been carried out for different preparations of cemented carbide surfaces as a function of relative velocity. In addition to the clear influence of the relative speed, an influence of the rake surface preparation could also be determined for medium speeds, as the figure shows for a jet machined and a polished surface. The explanation is to be found in the different adhesion behaviour, which, however, becomes much more similar again when the relative speeds are increased. At high relative speeds, small flat adherences are found on all tools and the frictional stress drops to a minimum. This indicates that a hardened intermediate layer is deposited, on which the workpiece material will slide off as it progresses. The influence of the surface thus fades into the background. With the help of these experiments, models can be generated to describe the frictional behaviour in FEM simulations.
In a further investigational setup, orthogonal cutting tests were carried out with the differently prepared rake faces. Thus, the influence of the surface topography on the friction behaviour between tool and chip with respect to the mechanical and thermal tool load and the adhesion tendency could be investigated.
Another goal of this project is to achieve an improved and realistic friction model for the Finite Element (FE) simulation of chip formation. In order to obtain realistic simulation results, proper input data for the material and frictional behaviour is needed. Especially the prediction of the passive forces shows high deviations, since these are mainly determined by the friction on the rake face. The experiments on friction characterisation have made it possible to develop models that describe the friction coefficient of the Coulomb model as a function of the tool surface and the relative velocity. Thus, the predictability of the process forces could already be significantly improved.
In the following investigations, the influence of temperature on friction will be characterised and integrated into the existing models. Furthermore, the thermal load of the chip formation zone as a function of the chip surface preparation and the cutting values is to be investigated. A realistic prediction of thermal loads has also been achieved.
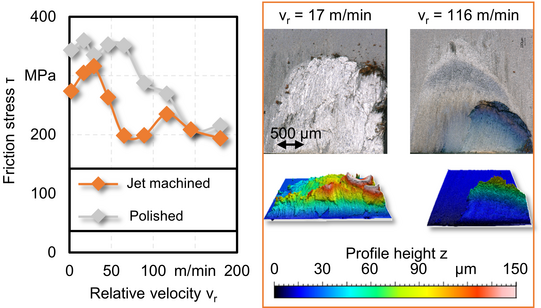