Simulation-Based Design of High-Performance Internal Grinding Processes
Due to the long effective contact time of the grinding grains, the complex contact conditions and the difficult-to-handle coolant support, the process layout of internal traverse and internal plunge grinding is still challenging. An alternative to internal cylindrical plunge-cut grinding and internal cylindrical longitudinal pendulum grinding is internal traverse grinding (ITG), which is characterised by high flexibility and economic efficiency.
For ITG, thin grinding wheels are used which are divided into two areas, a conical roughing zone and a cylindrical finishing zone. Electroplated CBN grinding wheels are used for the internal cylindrical machining of hardened steels, as these offer high productivity due to the large chip space and the aggressive grinding wheel topography. A significant increase in the chip removal rate can be realised by high-speed machining. In order to get a high surface quality, a touch-dressing process is used. A dressing diamond tool generates a plateau at the CBN grains on the finishing zone before the process, which results in minimal values of surface roughness depth (Rz ≈ 2µm). The contact zone in ITG is much smaller than the ones in other internal grinding processes. This leads to small cutting forces. However, this small contact zone is also the disadvantage of the process since the generated heat is concentrated on a small area and can cause thermal defects. It results in the alteration of the surface layer or dimension errors of the workpiece. This affects the function of the workpiece during its operation. In order to predict the influences of the heat on the workpiece’s properties, the thermal load must be determined. In addition, the manufacturing accuracy of the workpiece can be negatively affected by elastic deformation as a result of workpiece clamping as well as yielding of workpiece and tool spindles during machining. In order to achieve a high process reliability and high manufacturing accuracies, it is crucial to know these influencing factors, to be able to avoid them in advance.
In the previous project, a holistic simulation framework with three components was established by modelling the thermo-mechanical loads and their effects on the machining errors in different scales (fig.). Based on this, compensation strategies were achieved, reducing the machining error along the bore whole by 50 percent. The exception here was the discharge area of the workpiece, where a relatively large dimensional error remains due to the compliant spindles.
The objective of the current transfer project is the enhancement of the established holistic simulation framework to generate a prototypical solution for the industrial environment. Here, it is focused on the implementation of the spindle complaints and the grain related wear in the different components of the simulation framework of internal traverse grinding. Due to a close cooperation with the application partners, industry-relevant requirements for a simulation-based tool and process design are defined. The usage of the holistic simulation framework secures the optimal design of the grinding wheels as well as the generation of a compensated NC-path to reduce errors regarding the dimensions as well as the form. This allows the validity of the simulation system for industrial applications to be demonstrated by simulating extensive wear investigations and ramp-up processes under the changing process conditions in advance of the real processes. The coupled simulation system can be used for the process design and optimisation to avoid potential machining errors during internal traverse grinding operations.
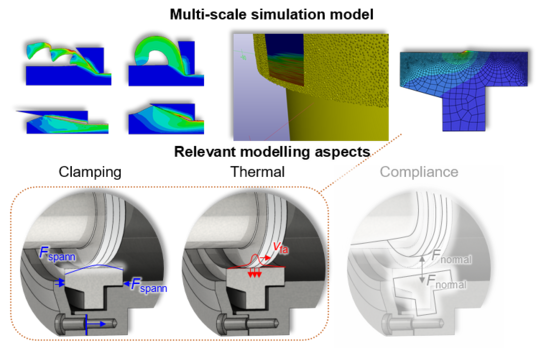